亚表面损伤产生的原理由于光学元件是由脆性材料加工而成,从生产到加工再到最后抛光过程的工艺比较复杂,所以在元件的加工过程中元件表面由于压力会不可避免的在表面以下产生划痕,杂质和微裂痕等损伤,这些被统称为光学元件的亚表面损伤。亚表面损伤的范围一般在光学元件表面以下几百纳米至几百微米深度处,根据亚表面损伤模型理论,光学元件结构分为以下四个部分:(1)抛光层:0.1到1μm,形成于抛光阶段;(2)缺陷层:1到100μm,形成于研磨加工阶段;(3)变形层:100到200μm,形成于元件成型阶段;(4)光学材料基体。[4],[5],[6],[7],[8]在实验过程中,我们发现光学元件的亚表面损伤,多数集中在1到100μm深度处的缺陷层位置。同时,在监测光学元件生产过程时,我们发现研磨过程对亚表面损伤的影响较大,并且研磨过程中对光学元件造成的损伤很难在抛光阶段进行修复,为了减少光学元件的亚表面损伤,必须对研磨过程中亚表面损伤进行严格的监控。33024
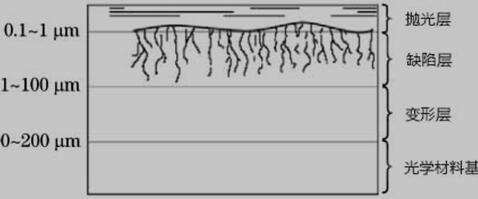
图1.3 光学材料亚表面层结构
2 测量亚表面损伤的一般检测方法
光学元件亚表面损伤作为光学元件及光学系统的重要参数之一,其测量方法自然会得到广泛的研究,下面简单说明一下这些测量方法。亚表面损伤的检测手段大致可以分成两类,分为破坏性检测和非破坏性检测。论文网
破坏性方法包括:
(1)化学蚀刻法[9]
化学蚀刻法是一种比较常用和方便的亚表面微裂痕检测手段,可用于晶体材料、熔融石英、玻璃等光学材料亚表面损伤检测。化学蚀刻法使用HF等酸性溶液与光学元件产生化学反应,通过逐层蚀刻元件表面获得蚀刻台阶,然后通过表面轮廓仪、光学显微镜观察亚表面损伤,同时得到亚表面损伤的深度。化学蚀刻法具有成本低、方便、直观等优点,是一种使用广泛的测量方法,但该方法的的缺点是精度不高,误差可能较大。
(2)截面显微法[12]
截面显微法是一种较为直接的亚表面损伤检测方法,可用于定性和定量检测光学元件研磨阶段的亚表面损伤。该方法通过光学显微镜对样品的磨削表面的垂直方向进行检测,从而得到亚表面损伤的结构和损伤的深度尺寸。为了可以精准的测量被测样品的亚表面损伤,样品制作过程中要保护好研磨表面的裂痕和抛光面与研磨表面相交的棱。截面显微法的缺点同样是精度不高,对损伤较小的样品检测比较困难。
图1.4 截面显微抛光图
(3)角度抛光法[11]
角度抛光法是一种最常用来检测半导体晶体的亚表面损伤的方法。其原理是先找到截面部分的亚表面损伤区域,再将该截面区域部分以α为夹角的斜截面上放大显示出来。由于可以通过光学显微镜观测到斜面上放大的亚表面损伤裂痕区域的大小设为S,最后利用公式 , 表示亚表面损伤。该方法测试精度可以达到μm级别。但该方法也有明显的缺点,就是只能对特定区域进行检测,并且斜面角度α的测量难度较大。
图1.5 角度抛光法
(4)磁流变抛光斑点法[12]
磁流变抛光斑点法是在磁流变抛光技术基础上提出的一种亚表面损伤检测方法,磁流变抛光斑点法利用磁流变抛光技术在光学元件表面进行抛光将亚表面损伤呈现出来,再利用化学溶液处理光学元件表面将裂痕展开,最后利用显微镜和轮廓仪分别检测亚表面损伤以及抛光斑点轮廓得到亚表面损伤深度。该方法不会对样品造成附加损伤,该方法相对于角度抛光法的损伤深度放大作用更加明显,因此更加适用于研磨抛光过程中的亚表面损伤检测。 测量亚表面损伤国内外研究现状:http://www.youerw.com/yanjiu/lunwen_29870.html